Pantex Blog
Celebrating 70 Years of Securing America
Seventy years ago this September, the first 500-pound bomb came off the assembly line at Pantex in Amarillo, Texas. And though the Plant’s mission has changed from weapons production to protection and preservation, the job of Securing America is as important today as it was in 1942.
A constant over time is the dedication of the Pantex workforce. Longevity speaks volumes, and the average tenure at Pantex is 15 years. This is high, according to a 2012 report from the Federal Bureau of Labor Statistics, because the manufacturing industry as a whole averages
just six years of service.
Malcolm Clack, Applied Technology specialist, holds the lowest-number identification badge, a designation meaning he’s worked at Pantex longer than any other employee. The history of the Plant through his eyes underscores the mystery of the mission.
When Clack came to the Pantex Ordinance Plant in 1958 as a guard, he worked three months while waiting for his clearance. During that time, nobody talked about what went on at the Plant. When his security clearance finally came through, Clack’s supervisor asked him to patrol an
area where he previously did not have access. Because no one was available to show him where to go, he was given a hand-drawn map.
On entering the first cell on Clack’s new patrol route−by himself at 2 a.m.− he clearly remembers the eerie hum of the air conditioner. And then he spotted it. Though he wasn’t sure, what little Clack knew about nuclear weapons led him to believe he’d encountered one first
hand. Most surprising, he said, was that nobody had spoken a word about it.
“After I got my clearance, coworkers began to talk. All I knew was that I was here to do a job, whether it was ‘making soap’ or bombs,” Clack said. “People do good work at Pantex and it’s something that the country needs. I feel like we’re protecting the country so people
won’t mess with us.”
Administrative Specialist Linell Carter holds the distinction of being the woman with the lowest badge number at Pantex. Though her service time includes a break, Carter is in her 26th year. Over the years, she held various positions, but among Carter’s favorite was her
role as union steward in 1967.
“The life-changing things that the union was able to accomplish were very exciting,” Carter said. “We were able to get equal treatment for minority races, to kind of slow down sexual harassment, women to be able to have any job and pay just like the men, men to be able to take
leave when their babies were born just like the mother was allowed and several other accomplishments.”
During the Cold War, Carter said it was great to be a part of the protection of our country and our freedom. “The weapons that we provided gave such peace and stability to our troops that so many of them were able to come back to the U.S. to their lives here. All of it was totally
spine tingling,” she said.
Added George West, retired physicist with 42 years of service, “It cannot be denied that Pantex played a major role in winning the Cold War. If we did not do anything else, we convinced the Soviets, among others, that we had nuclear weapons, and that they were going to work
if we were forced to use them.”
High Explosives Pressing Facility Designed Using 3D Modeling
Ability to course correct at design sets new enterprise standard
Operations at half a dozen aging Pantex buildings will come together under one roof at the High Explosives Pressing Facility (HEPF), which is expected to be complete in November 2013. The new facility will greatly reduce the movement of high explosives at Pantex, increasing safety and aiding production, as high explosives moves can restrict other Plant operations.
What sets HEPF apart from other facilities constructed at Pantex is the technological advances in design on which engineers have capitalized. The 3D Building Information Model (BIM) approach, provided by B&W Pantex and CH2M Hill, was employed to ensure all aspects of the facility were captured in the design. The design tool optimizes coordination in systems-intensive facilities
and allows the team to “see” critical interfaces between structure, systems, and operating equipment.
“It enables us to derive material quantities both as total and installed counts, compare against the contractor’s invoices and review proposed design changes as well as field deviances to keep control of the overall and detailed design,” said Steve Forman, project engineer. “This is
groundbreaking for maintaining construction progress.”
The HEPF 3D BIM was so successful during the design phase of the project that DOE supported funding to maintain the 3D BIM throughout the four-year construction period. This allows for the model to be updated daily, weekly or monthly, as needed, to keep it an ongoing “as-built” that reflects real-time changes in the field. On project completion, Pantex Maintenance will use the BIM to enhance maintenance capabilities throughout the life of the facility, which should result
in significant cost savings, according to David McCown, maintenance manager.
“The 3D BIM made it possible to correct utility and system conflicts during the design phase of the project and eliminated 500 Requests for Information during construction that the contractor would have submitted, which would have impacted cost and schedule of the project and ultimately startup of the facility. An independent government estimate determined that these
cost savings were between $7 and $10 million dollars,” said Rodney Whisenhunt, project manager.
According to Fabian Thomas, NNSA Production Office federal project director, the 3D design has pioneered a new approach to the design and construction of future industrial facilities. “The HEPF 3D BIM is the new standard and has changed the method that Line Item Projects, those greater than $20 million, will be planned and executed at Pantex as well as throughout the NNSA,” he said.
HEPF 3D BIM was selected as a finalist within the category “Innovation in Industrial Facilities” in the Bentley BE Awards, ranking it one of the top three design projects in the competition for Best Practices for Sustaining Infrastructure, according to Robert Cole, program manager.
The HEPF project, constructed by Kiewit, managed by the U.S. Army Corps of Engineers and supported by the B&W Pantex project management team, is on budget and on schedule. Startup and commissioning are projected to finish ahead of schedule in April 2016.
When completed, the HEPF will provide increased levels of protection for workers, improve pressing operation efficiencies, eliminate single points of failure for the pressing process and support the U.S. Department of Energy’s High Explosives Center of Excellence for manufacturing at Pantex.
New Method of Polyurethane Mixing Brings New Opportunities
by Paul Lamonica, 2012 Summer Intern
This year, the B&W Pantex Plastics Shop began formulating a new method of mixing polyurethane molded parts for explosives, coatings, seals, cushions, tool covers and more. The old method consisted of mixing the components in a generic “ice cream bucket.” After the correct amounts of materials were mixed together, the mixture would be carefully injected into the mold to form the needed part.
At first glance, this process appears simple, but it took approximately two to three hours to make one mold. In addition, the cleaning process could expose people to hazardous chemicals. Some of the molds formed bubbles and voids after the mixture was injected. After rising concerns about the old mixing method, the Plastics Shop knew that it was time to start researching better
alternatives.
Months were spent researching solutions, and the group discovered a revolutionary type of mixer. This eco-friendly system, known as the dynamic mixer, resolved all of the previous problems with the ice-cream-bucket method.
When the dynamic mixer arrived in February, the Plastics Shop teamed with West Texas A&M University (WTAMU) to give students the opportunity to be engaged with this research. The mixer is residing at the university for research purposes, and Stephanie Steelman, a polymer chemist in the Explosives Technology Division, is the project manager and principal investigator for the
WTAMU collaboration.
Devin Cook and Matt Dolezal, both mechanical engineering majors at WTAMU, have been working on this project since the beginning of this year.
Cook, a senior, has been working on the mold designs and optimizing software specifically for the dynamic mixer. “Engineering today is mainly done on computer, and having knowledge of all this software and technology will benefit me in the future,” said Cook.
Dolezal, who graduated from WTAMU in May, has been working with the mechanical engineering and chemistry research of the project, although both work together on all areas of the project. “I really enjoy how much I’ve learned from this experience; I think the knowledge and
skill sets I’ve gained will help me greatly starting my career,” said Dolezal.
Using the dynamic mixer, it now takes only a few minutes to produce each mold. There is minimal cleanup with no exposure to chemicals and there are no bubbles within the mold. The largest mold, which takes about five pounds of material, requires only three to four minutes to fill.
The project will be finished later this year, and the mixer will reside at Pantex starting sometime in March. “The new mixer will save the Plant money in the form of time, raw materials and personnel resources,” Steelman said.
Each year, the old method cost to the Plant is approximately $100,000 just in packaging and weighing materials for the Plastics Shop to use. The dynamic mixer will allow the Plastics Shop to decrease raw material and rejected parts by at least 80 percent and reduce employee hours and resources repackaging raw materials, said Steelman.
Summer Interns Pursue Booming Business
by Lauren O'Brien, 2012 Summer Intern
The summer intern program is one of three student work programs B&W Pantex offers. It has been implemented nine out of the 11 years since B&W Pantex took over the management and operation of the Plant in 2001, and the Explosives Technology Division has had at least one intern each year.
Mike Whitley, program manager in the High Explosives Engineering and Physics Department, said several summer interns have come back multiple times, and some, like Amanda Wiggins, who is now a section manager, have returned as full-time employees. Whitley believes this program is “definitely” beneficial to the organization.
“It gives interns exposure to what we do out here at Pantex,” he said.
One such intern, Charmaine Gobert, a first-time intern for Explosives Technology, is attending McNeese University with a major in chemical engineering. During her internship, she worked on developing piping and instrumentation diagrams for formulation processes. She also has been researching cost and design aspects for future synthesis operations. Through this experience, she enjoyed “being able to see [her] books come to life” as she worked.
“This internship has allowed me to make more sense of the principles, equipment and techniques I’ve only been able to see on paper,” Gobert said.
Another intern, Edward Flores, is majoring in mechanical engineering at Texas Tech University. This summer, his second at Pantex, he worked on a project involving a rigid-arm pendulum.
“The [apparatus] is used for skid testing of high explosives (HE). A piece of HE that’s placed in the pendulum arm is dropped at different angles and tested to see the ignition point and the ignition size of the HE after the rubbing of the two surfaces,” Flores said.
He enjoys working on Professional Engineer (Pro-E), which is a program that allows him to create two-dimensional drawings, three-dimensional images and complete virtual assemblies.
“My favorite part of the internship is getting to see several different explosions at the Firing Sites,” he said.
Both Gobert and Flores would like to return as full-time employees after they graduate this year.
“I have really grown to enjoy the environment Pantex offers,” Gobert said. “The work performed here is very interesting, and the people are genuinely quite friendly and helpful.”
John Woolery, B&W Pantex President and General Manager, believes the internship program is “super valuable” to the organization as it looks for prospective employees.
“We get a chance to check students out… and make sure we get the best and brightest,” he said.
Smart Cookies
Pantex Engineers Host Workshop for Girl Scouts
Don’t tell the young women engineers at Pantex that engineering is a career for men only. They just spent their Saturday making sure that old-fashioned notion winds up in the dustbin of history.
The half dozen young Pantexans, all around their mid-20s, put on a workshop called “Smart Cookies” to show more than 40 Girl Scouts that engineering is a great career for everyone, especially young women.
“There is no doubt that engineering has traditionally been viewed as a man’s career field, but that is changing,” said Savannah Gates, a process engineer at Pantex. “We want to continue that transformation by encouraging these young women to join us in the engineering field.”
Gates was joined by her fellow engineers Ashley Latta, Brandy Ramirez, Sarah Cox, Jessie Phifer, Raquel Barrera and Halianne Crawford in organizing the workshop. The Pantex engineers demonstrated the principles of a variety of types of engineering, including electrical, mechanical, civil and chemical.
The activities ranged from making a homemade battery from foil, pennies and paper towels soaked in a vinegar-salt solution to building cars powered by the kinetic energy of a mousetrap. The mousetrap cars proved so entertaining for the Girl Scouts, and took up so much of the day, that the women engineers were forced to postpone several other engineering activities that will be used as the basis of a second workshop later this year.
“It was amazing to see how excited these young ladies were to learn about engineering,” Phifer said. “You could tell our message really resonated with them, so I’m hopeful that some of these girls might be working with us as engineers at Pantex one day.”
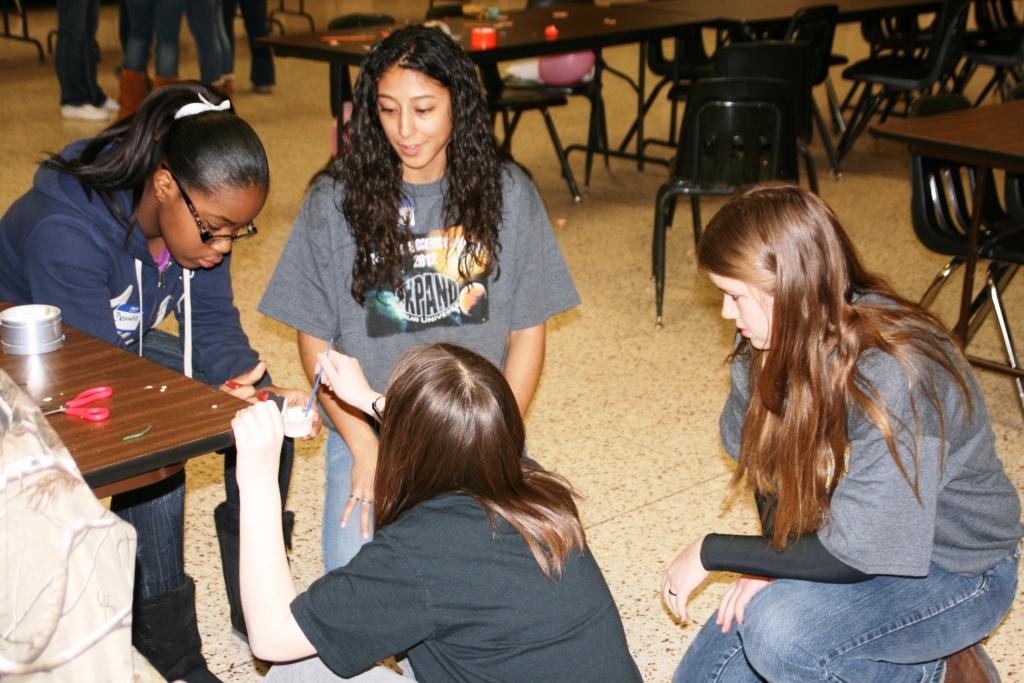
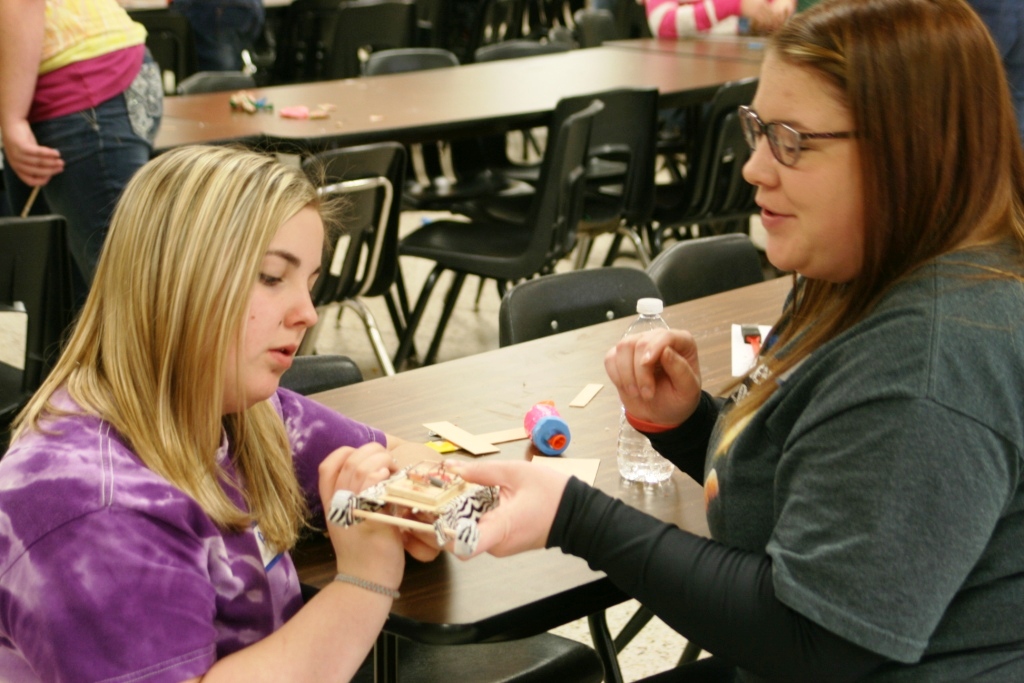